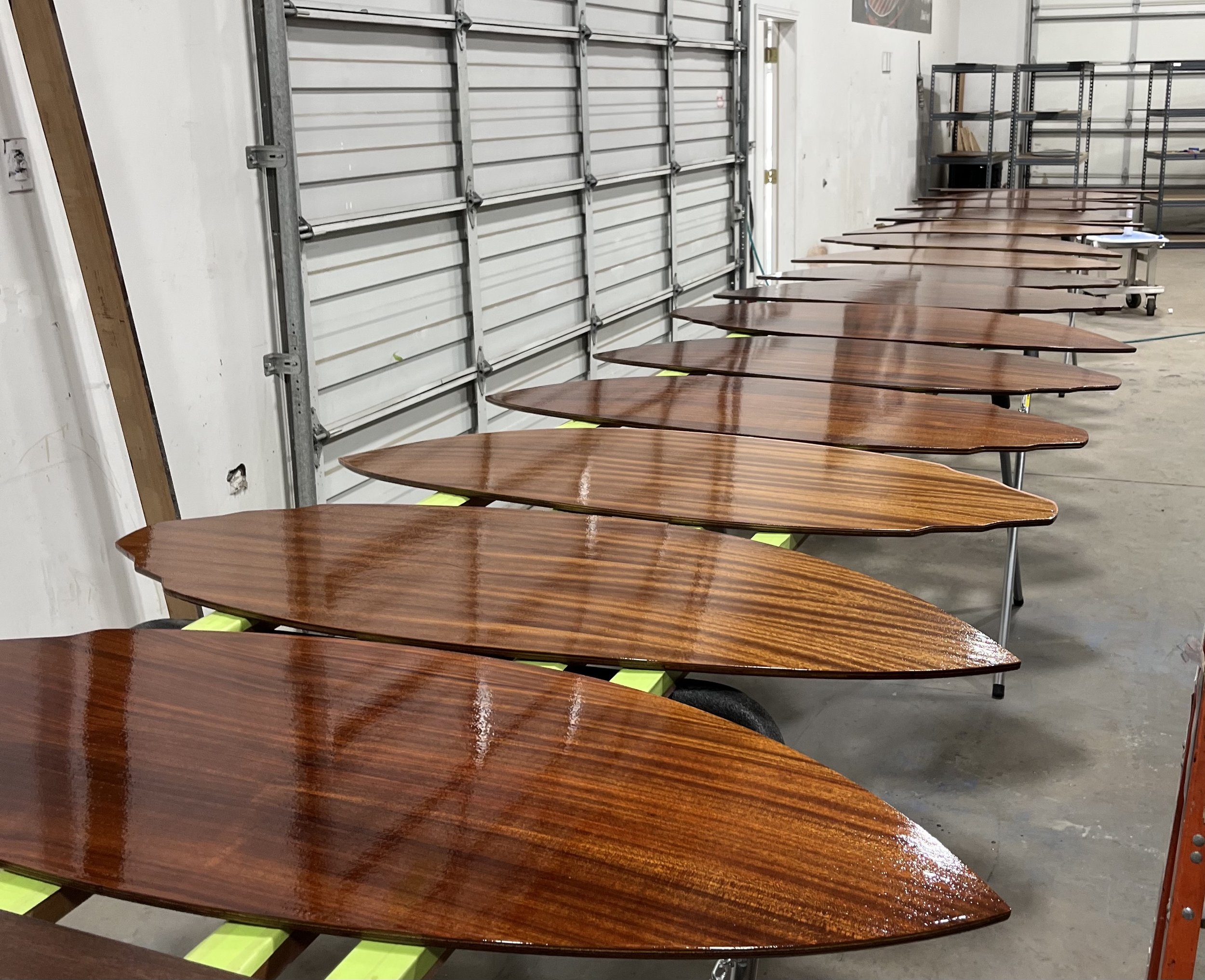
The Build Process
-
All new boards are made from a solid core of cnc shaped plywood blanks with a veneer top and bottom
-
Once all 5 layers are cut, the layers are then coated with epoxy on each side, and pressed under 20 tons of pressure for 24 hrs.
-
The board has cured after 24 hrs. It is then released from the press and clamped into a routing pattern to trim excess material
-
The desired shape of the board is routed/sanded to specs. Ready for its first coat of stain.
-
Once the board is sanded to finish quality. It is then stained and sealed on both sides
-
The board has been treated with sealer, it is now ready for the first layers of clearcoat to be applied
-
When there are enough base layers applied to make the board finish appear flat, a custom painted design is applied
-
Now that the design is applied, the final layers of clearcoat are put on.
-
Final edge paint layers and clear coats are applied.
-
Both clearcoated sides are sanded flat, then have a final clear coat sprayed. Then the board is buffed to perfection.
-
The trackpad and rudder(s) are installed.
-
The board is now finished and ready for riding
-
(If applicable) water testing may take place!